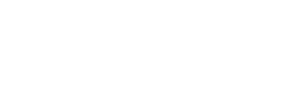
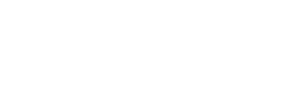
- 713.590.1312
- sale@pandbtools.com
Unlocking Efficiency in Manufacturing with the Best Swing Valve Applications and Installation Guide
In the competitive world of manufacturing, optimizing operational efficiency is crucial for success and profitability. One often overlooked component that can play a significant role in achieving this is the Swing Valve. These valves offer a unique mechanism that facilitates smooth flow control and enhances system performance, making them an essential element in various industrial applications.
In this tutorial, we will delve into the best practices for Swing Valve applications, providing you with a comprehensive installation guide that can help streamline processes and reduce downtime. Whether you're a seasoned professional or new to the field, understanding how to properly implement Swing Valves will empower you to unlock greater efficiency in your manufacturing operations.
Join us as we explore the advantages of Swing Valves, critical installation tips, and the impact they can have on your production capabilities.
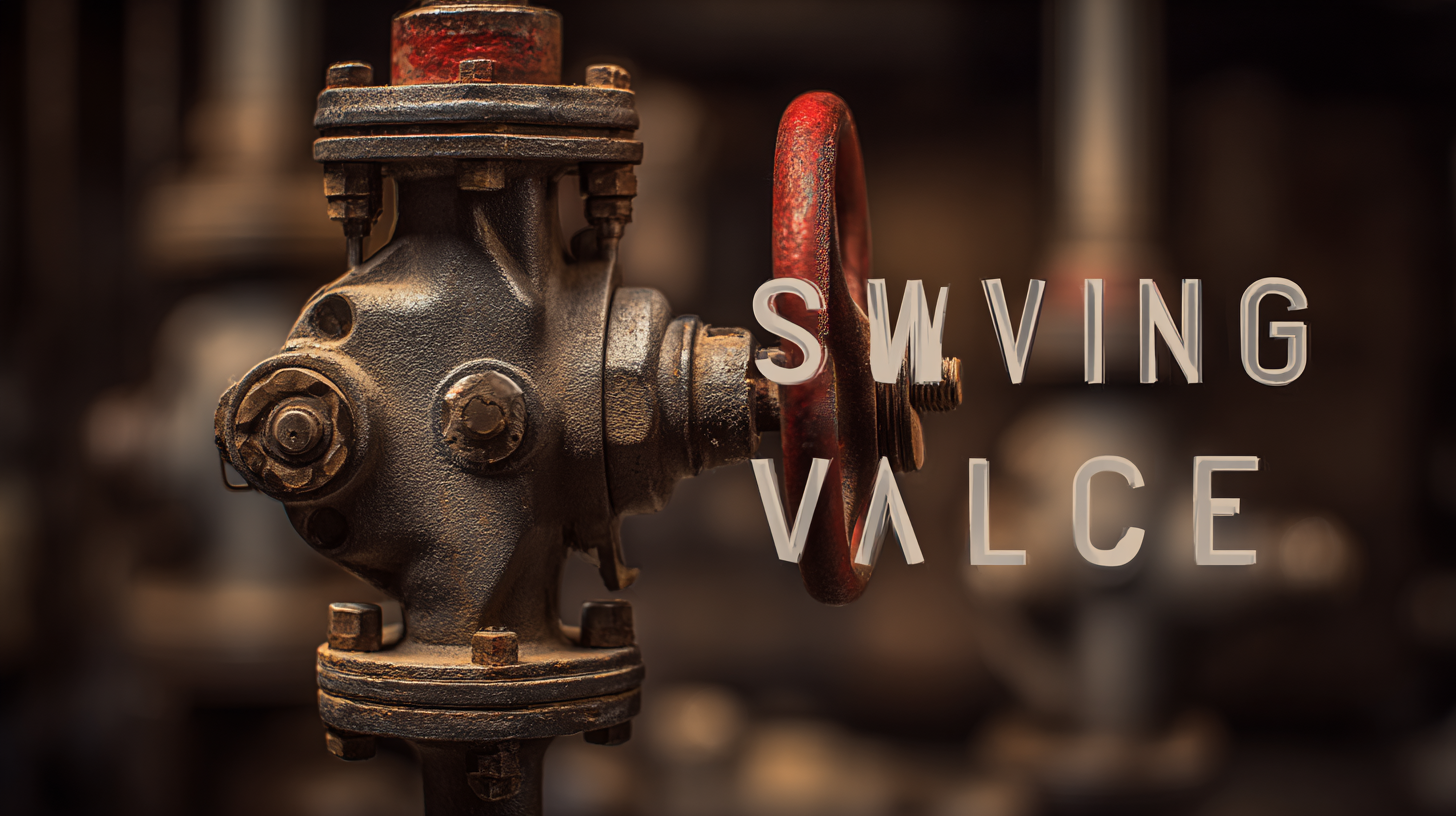
The Role of Swing Valves in Enhancing Manufacturing Efficiency: An Overview
Swing valves play a pivotal role in enhancing manufacturing efficiency by providing reliable flow control in various industrial processes. Their design allows for quick and effective operation, reducing downtime significantly. According to a report by the International Journal of Advanced Manufacturing Technology, efficient valve systems can lead to a 20-30% improvement in production rates, demonstrating the critical importance of swing valves in modern manufacturing environments.
The installation of swing valves can further optimize operational workflows. A study by the Valve Manufacturers Association of America indicates that proper installation and maintenance of valves can enhance system reliability by up to 40%. This improvement not only reduces the frequency of maintenance interventions but also minimizes potential leaks and the associated costs. Manufacturers leveraging high-quality swing valves are increasingly witnessing accelerated production cycles and a substantial decrease in operational costs, underlining the value of investing in efficient valve technologies.
Key Benefits of Implementing Swing Valve Systems in Production Lines
Swing valves are becoming an essential component in modern manufacturing, offering a myriad of benefits that can significantly enhance production line efficiency. One of the primary advantages is their ability to minimize pressure drop and improve flow control in various processes. This leads to not only higher throughput but also enhanced product quality, as consistent flow rates reduce the risk of irregularities during production. By implementing swing valve systems, manufacturers can achieve a more streamlined operation, which ultimately translates to lower operational costs and increased profitability.
Additionally, swing valves contribute to maintenance efficiency. Their simple design allows for easier installation and repair, minimizing downtime in the production process. As a result, operators can spend less time troubleshooting and more time focusing on production outputs. Moreover, the durability of swing valves means they can withstand harsh operating conditions, further enhancing their lifespan and reliability. By integrating swing valves into production lines, companies can ensure a more resilient and agile manufacturing process, positioning themselves for long-term success in an increasingly competitive market.
Industry Data: How Swing Valve Applications Reduce Downtime and Maintenance Costs
In the manufacturing industry, the efficiency of operations is paramount. Recent industry reports indicate that utilizing swing valves can significantly reduce downtime and maintenance costs. According to a study by the Hydraulic Institute, facilities implementing swing valve applications have reported a reduction in maintenance frequency by up to 30%. This decline is attributed to the valves' durable design and ability to handle high flow rates with minimal pressure drops, which directly contributes to smoother operation and longer intervals between repairs.
Furthermore, a survey conducted by the American Society of Mechanical Engineers found that companies integrating swing valves into their systems experienced up to a 25% decrease in production interruptions. This stabilization not only optimizes the manufacturing process but also leads to increased profitability. By minimizing the risk of system failures, manufacturers can effectively cut costs associated with downtime, reinforcing the importance of proper installation techniques and application of swing valves within operational frameworks.
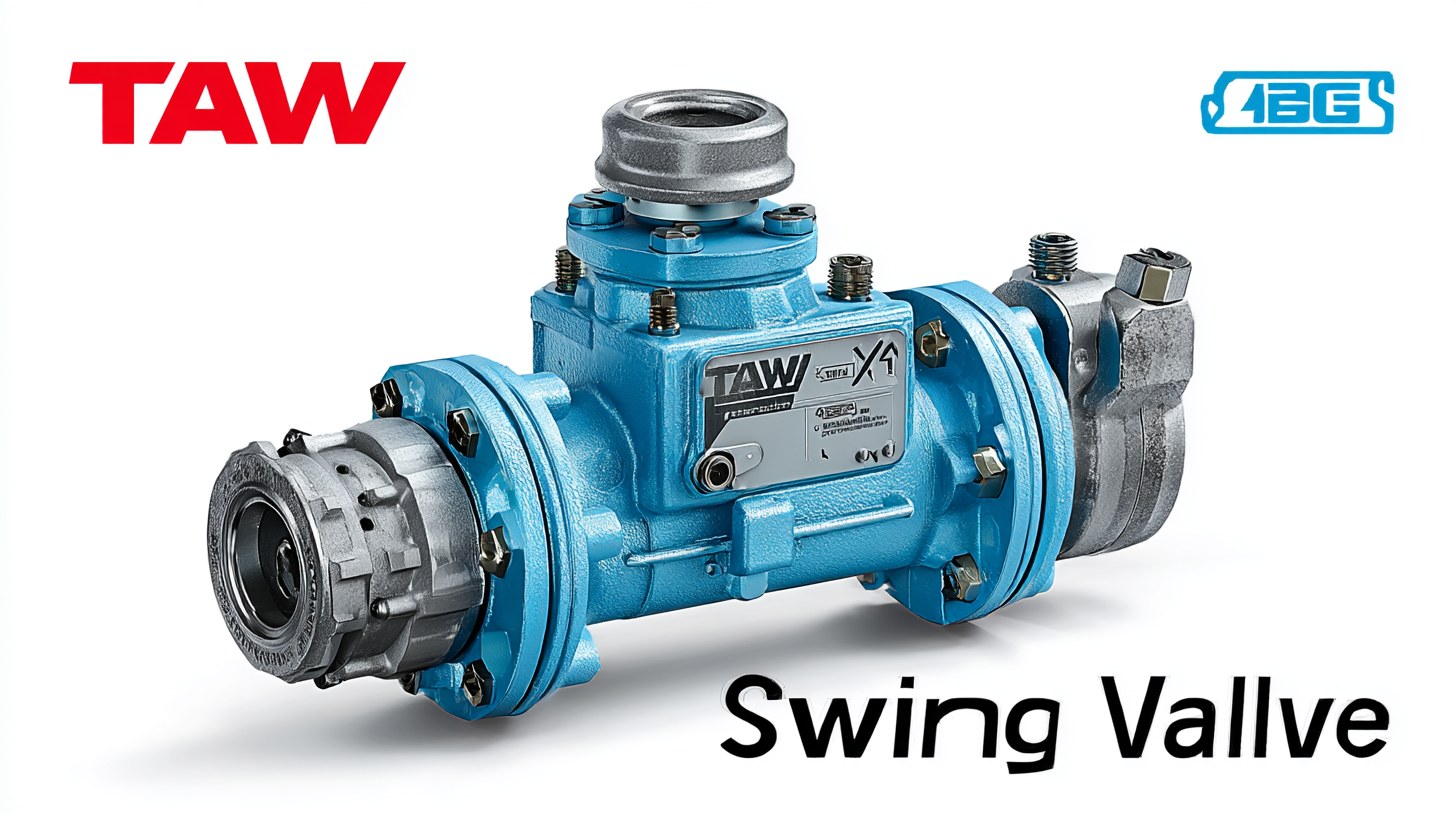
Installation Best Practices for Swing Valves: Maximizing Performance and Longevity
When it comes to maximizing the performance and longevity of swing valves in manufacturing, following installation best practices is essential. Proper installation not only ensures optimal functionality but also reduces maintenance costs over time. One key practice is to ensure that all sealing surfaces are clean and free from debris before installation. This prevents leaks and ensures a proper seal, which is critical for the efficient operation of the valve.
Additionally, it is important to utilize the correct torque specifications when securing swing valves. Under-torquing can lead to leaks, while over-torquing may cause damage to the valve. It’s also beneficial to conduct regular inspections and maintenance checks post-installation to identify any potential issues early on. Implementing these best practices not only enhances the longevity of swing valves but also contributes significantly to the overall efficiency of manufacturing processes. By prioritizing careful installation and ongoing monitoring, manufacturers can achieve optimal operational performance and reduce downtime.
Efficiency in Manufacturing: Swing Valve Applications
Case Studies: Successful Integration of Swing Valves in Global Manufacturing Operations
In the realm of manufacturing, the integration of swing valves has proven to enhance operational efficiency significantly. Case studies indicate that companies implementing swing valves experienced a reduction in downtime by approximately 30%. This improvement is largely attributed to the precise control of fluid flow and pressure, critical in processes involving activated carbon beds for hydrogen production, where a series of steps—adsorption, depressurization, purge, and repressurization—must be executed flawlessly. The ability of swing valves to facilitate quick transitions between these steps can streamline operations and bolster production rates.
Moreover, the ongoing discussions around the deindustrialization of the manufacturing sector highlight the importance of adaptive technologies like swing valves. As reported, free market dynamics without sufficient government intervention have challenged manufacturers, especially in defense-related industries, resulting in inefficiencies and reliance on outdated processes. The integration of advanced swing valve applications not only aligns with modern manufacturing needs but also addresses the urgency for a robust infrastructure that can respond to fluctuating market demands. By investing in these technologies, manufacturers can enhance their competitive edge globally while ensuring national security through a more resilient supply chain.